Last updated on April 29th, 2020 at 06:29 pm
Analog Trim Gauge Conversion For Mercury Optimax Outboards. Volvo trim motor wiring diagram full mercruiser indicator gauge i bought a two wire power tilt unit for 1983 80 hp mercury the 2 and harness sender troubleshooting drive trims down but sending questions resistor moderated 90 pontoon have 150 blackmax replacing your limit pump smartcraft offsonly com evinrude e tec analog conversion. Pro-Trim is a “bolt-on” for most SeaStar Solutions steering systems and is attractively packaged, with everything you need. Also suitable for use with Command 200 rack & pinion steering, and it’s the only trim switch recommended for SeaStar® and SeaStar PRO® hydraulic steering systems! Teleflex PT1000P Single Function Control Pro Trim,Trim Teleflex PT1000P Single Function Control Pro,: Teleflex PT1000P Single Function Control Pro Trim: Telflex Pro Trim: Sports & Outdoors,Fast Free Shipping,Latest hottest promotions,The Hottest Design,Fast (7-Day) Free Shipping,Buy an official website online here! Trim installation with paint: $3.50 per linear foot, including materials. Trim installation without paint: $3.25 per linear foot, including materials. Average cost to install trim in a 10x10-foot bedroom: $500 for one window and one door, including labor, materials and paint.
Are you needing to replace your boat steering cable? Then you’ve come to the right place. However, if you are a beginner with marine hydraulic steering systems, we recommend that you first check out our SeaStar Solutions Hydraulic Steering Guide.
Skip To:
Boat Steering Cable Replacement Cost Estimate
Boat steering cable replacement cost at a dealership will run you anywhere from $300-$650, depending on the make and model of your boat. However, many folks opt to do it themselves, as the boat steering cable replacement job is relatively easy.
How To Install Teleflex Pro Trim Machine
If you do go the DIY route for your marine steering cable replacement, you can find the best and usually cheapest replacement Teleflex cables on Amazon.
Here are some of the best boat steering cables available for sale.
BOAT STEERING CABLE | BRAND & MODEL | LENGTH (ft) | RATING | LINKS | PRICE & AVAILABILITY |
---|---|---|---|---|---|
SeaStar SSC12412 | 12 | 4.8 | Reviews | Check Price | |
SeaStar SSC13413 | 13 | 4.5 | Reviews | Check Price | |
Uflex M66X14 | 14 | 5.0 | Reviews | Check Price | |
Teleflex 14-Feet | 14 | 4.5 | Reviews | Check Price | |
SeaStar SSC13516 | 16 | 4.9 | Reviews | Check Price |
Teleflex Steering Cable Vs. SeaStar Steering Cable
If you have been looking for a boat steering cable replacement online, you have probably been seeing Teleflex cables and SeaStar cables. For example, we have both listed in the table above. Naturally, you may be wondering what is the difference between a Teleflex steering cable and a SeaStar Steering Cable. The answer is “not much”.
In February of 2013, Teleflex announced that it was changing it’s name to SeaStar Solutions. So, when you come across a Teleflex steering cable online, you are actually looking at a cable made by SeaStar Solutions. It seems that people are simply still more apt to search for Teleflex cables, since that is what they are accustomed to looking for. Therefore, a lot of sellers are still selling the cables as a Teleflex steering cable.
Boat Steering Cable Installation Tips
The first step to boat steering cable installation is to be certain that you’ve measured properly and ordered the proper length of steering cable. Pro tip: the number 1 reason for marine steering cable returns is “wrong cable length ordered”.
Follow the boat steering cable installation instructions that came with your cable or kit. Doing so will allow for the maximum reliability and performance of the cable.
Allowing for generous steering cable bends will lengthen the lifespan of the cable. A stiffer cable with tighter bends is subject to more stress, and therefore a reduced cable life.
Replace, rather than reuse, all worn out steering mounting and connection components. Be sure to select the proper replacement parts which are designed specifically for the application. Whatever you do, do not attempt to substitute parts.
When you get to the point of installing the steering cable at the boat’s engine end, make sure that you lubricate the telescopic ram with generous amounts of a good quality, Lithium-based waterproof grease. This step is TREMENDOUSLY crucial if the boat steering cable is connected via the boat’s engine tilt tube.
There is no substitute for regular annual boat steering cable maintenance procedures.
Boat Steering Cable Maintenance Guide
If you are either getting your boat ready for winter or getting it ready for the upcoming boating season, boat steering cable maintenance should be an integral part of your annual boating maintenance ritual. If you don’t keep your marine steering cable in good condition by doing your boat steering cable maintenance, your boat will have rough handling, or possibly a complete loss of steering.
While boat steering cable maintenance requirements will vary slightly depending on the boat, servicing the marine steering cables is usually very similar across all makes and models. Follow the three easy steps below.
Items you will need prior to performing marine steering cable maintenance:
- Heavy marine grease
- Gun oil, machine oil, or a similar lightweight oil
- Grease gun
- Open end wrench
Step 1 – Retract the boat steering cable into the tilt tube by turning the steering wheel as far as you can to one side. Firmly press the injector fitting of your grease gun onto the boat’s steering cable nipple (grease fitting) and squeeze or pump the grease gun’s handle in order to generously lubricate the steering cable. Keep pumping the grease until it oozes out around the gun’s injector fitting and the nipple.
Step 2 – Ensure that the steering link rod fasteners are tight by gently trying to shake them using an open end wrench. It’s important to check that the nylon insert lock nut is resting on top of the steering link rod. Also be sure to check that the washer is securely seated underneath the nylon insert lock nut. You will notice that the boat steering cable is affixed to the boat’s steering link rod.
Step 3 – Lastly, using gun oil, machine oil, or a similar type of lightweight oil, lubricate the steering link rod pivot points.
Boat Steering Cable Boot Description
A boat steering cable boot is usually made of rubber and is designed to be installed on top of the output end of the boat steering cable on the engine end. The boat steering cable boot provides complete protection from weather and other elements, and it also helps to prevent the lubrication on the cable from being washed away.
A boat steering cable boot will run you about $10-$50, depending upon which one you need. Click here to check prices on the boat steering cable boot for your boat.
Is Your Boat Steering Cable Stuck?
Sometimes, if your boat has been sitting for an extended period of time, your boat steering cable may become stuck. There are a couple of different methods to try to resolve your boat steering cable being stuck.
You could first try using a little WD-40 and a rubber mallet to see if you can loosen up the stuck boat steering cable. If that doesn’t work, you can follow the instructions in this video we found on how to deal with a boat steering cable stuck.
Return to our homepage.
Give your project a finished look by learning about some of the finer points of finish carpentry.

Photo: istockphoto.com
The trim installation stage of any interior project can be tremendously rewarding. Baseboard and crown molding can turn a basic drywall and paint project into a polished work of art. If you’ve always admired fine trim work but aren’t sure where to start, you’re probably feeling a little intimidated. There’s no need to fret. By familiarizing yourself with these tips for installing trim, you’ll be well on your way to a professional finish that you can take pride in.
RELATED: 9 Ways to Dress Up a Room with Molding
1. Gather the right tools for installing trim.
Making accurate cuts that result in tightly mitered corners can be a challenge without a compound miter saw. Likewise, hand-nailing baseboards and crown molding can be a true labor. While having a full complement of tools would be ideal, it may not be possible for you. At the least, you’ll want to purchase, rent, and/or borrow the following tools:
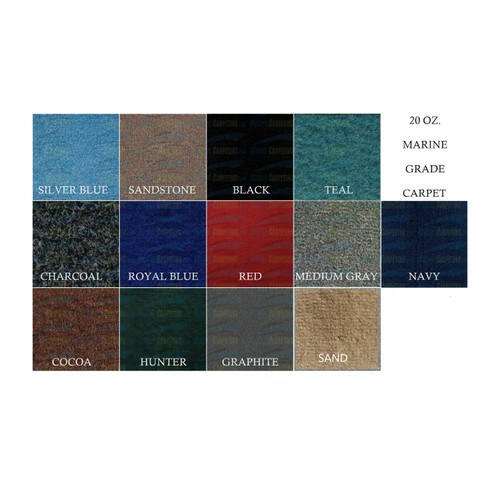
- Compound miter saw
- Air compressor with a hose
The most important tool of all is a sharp pencil. A high-quality pencil will be worth its weight in gold on any finish carpentry project. The difference between a good and great trim installation may be less than 1/32 of an inch, so make sure you keep your pencil sharp to achieve the best results.
2. Calculate how much trim you’ll need, and buy a bit more than you think you need.
Don’t let a material miscalculation delay your project. You’ll want to purchase about 20 percent extra material to account for mistakes, offcuts, and overlapping joints. Luckily, there’s an easy rule of thumb for determining how much baseboard or crown molding you need. Measure the length of each wall from corner to corner, subtracting any openings for doors or closets. Now double the value for one of the shorter walls. (By doubling the value of one of the walls, you’re leaving yourself a buffer.) Add up these measurements to find how much trim to purchase for your project.
Tip: Your local home improvement store will sell baseboard and crown molding in 8-foot and 12-foot lengths, so you should be able to trim an average 16- to 20-foot living room wall with two pieces of molding.
Photo: istockphoto.com
3. Use a compound miter saw to make accurate cuts.
Compound miter saws make quick work of cutting trim. These power tools have fast-spinning saw blades that cut through wood quickly and accurately. Compound miter saws have rotating beds with preset detents that click into place at the most common cutting angles. Even beyond that, they also tilt from side to side in order to cut compound angles for complicated crown molding joints.

Use a sharp pencil to make an accurate mark on the board where you need to cut. Without triggering the saw, lower the blade so you can line it up precisely with your mark. Once you’re satisfied with the blade’s alignment, lift the saw up so the blade isn’t touching the workpiece. Now trigger the saw, let the blade get up to speed, and carefully lower it into your trim board. Once the sawdust settles, you should have an accurately-cut piece of trim.
The procedure for cutting mitered angles is similar, but they require you to set the saw to the proper angle. These saws have handles that release the saw bed and allow you to turn it to the appropriate angle. For a 90-degree corner, you’ll want to set the saw to the appropriate 45-degree detent. Once you lock the bed back into place, you can proceed with your cut as normal.
Remember to pay attention to which side of the 90-degree mark that you set your saw, as this will determine whether you’re making an inside or outside cut. A board to the left of the saw with a negative 45-degree cut will result in a miter for an inside corner, while a positive 45-degree cut is meant for an outside corner. If you’re cutting your board to the right of the saw blade, reverse these rules.
For safety’s sake, be mindful of where your hands and fingers are in relation to the blade. Also, make sure you’re wearing safety glasses.
Photo: istockphoto.com
4. Get to know the three types of joints used when installing trim.
When it comes time to install trim around the corners of your room or walls longer than the typical run of trim, use these three joints.
- Coped joints: Coped joints are ideal for inside corners. Once cut at the appropriate inside angle (typically 45 degrees), the profile of the molding is followed closely with a coping saw. The saw should be held at an angle to back-cut the material slightly. The resulting pattern then fits precisely over the adjacent trim piece, creating a puzzle piece-like fit.
- Miter joints: Outside corners can be formed by cutting two boards at 45 degrees and fitting them together at a 90-degree angle where two walls meet. Inside angles can be cut using the same procedure, but most professionals prefer the coped method.
- Scarf joints:Make two shorter boards appear as one long piece by using a scarf joint. Begin by cutting the ends of two boards with overlapping 45-degree angles across their faces. When installing these boards on the wall, marry these two angles to make the joint disappear. Be sure to nail through the joint for the best results.
With any of these joints, you may still find a slight gap that requires additional work. Placing shims between the baseboard and the wall is a great way to close a small gap in an inside corner. For an outside corner, gluing and nailing through the joint before nailing to the wall will provide the best long-term results. It’s also a good idea to run a bead of caulk along the length of your moldings to finish the look and hide small gaps.
How To Install Teleflex Pro Trim System
Photo: istockphoto.com
5. Paint your trim before you install it to save time and energy.
Painting crown molding on the wall is likely to leave you sore from raising your arms overhead for hours. Similarly, painting baseboards while resting your knees on the hard flooring is the pits. Painting before installing trim can be a major energy and time saver, provided you have the space to do it.
For the best results, purchase pre-primed boards whenever possible. Lay trim boards across a pair of sawhorses. Use a brush, roller, sprayer, or some combination of all three to paint your boards before your trim installation begins. Do this for two to three coats to achieve a great finish.
Photo: istockphoto.com
6. Hide nail holes using wood filler and sandpaper.
When you’re happy with how your corner looks, nail into the lower 1½ inch of the trim with 2-inch finishing nails spaced roughly 16 inches apart. Nailing into the lower third of the molding increases the chance that you’ll hit the bottom plate inside of the wall. If installing crown molding, you’ll want to nail into the joists and studs at the top and bottom of the molding, which are usually every 16 inches. Save leftover paint (or stain) for after you’ve nailed the trim in place for touch-ups.
Camouflage those nail holes with a wood filler until they’re level with the wood, then paint or stain for the best-looking results. Apply a small amount of the filler with the tip of your finger and to each nail hole. Wait approximately two hours for the filler to cure before using a sheet of 220-grit sandpaper to lightly sand away the excess material. This will leave a smooth finish and make the holes disappear. Just touch it up with paint or stain, and your project is complete.